751 Gateway is a recently completed core and shell project located in South San Francisco. The new research and development building replaced a surface parking lot and is an addition to an existing eight-building campus. Construction of 751 Gateway expanded the campus to 1.1 million square feet.
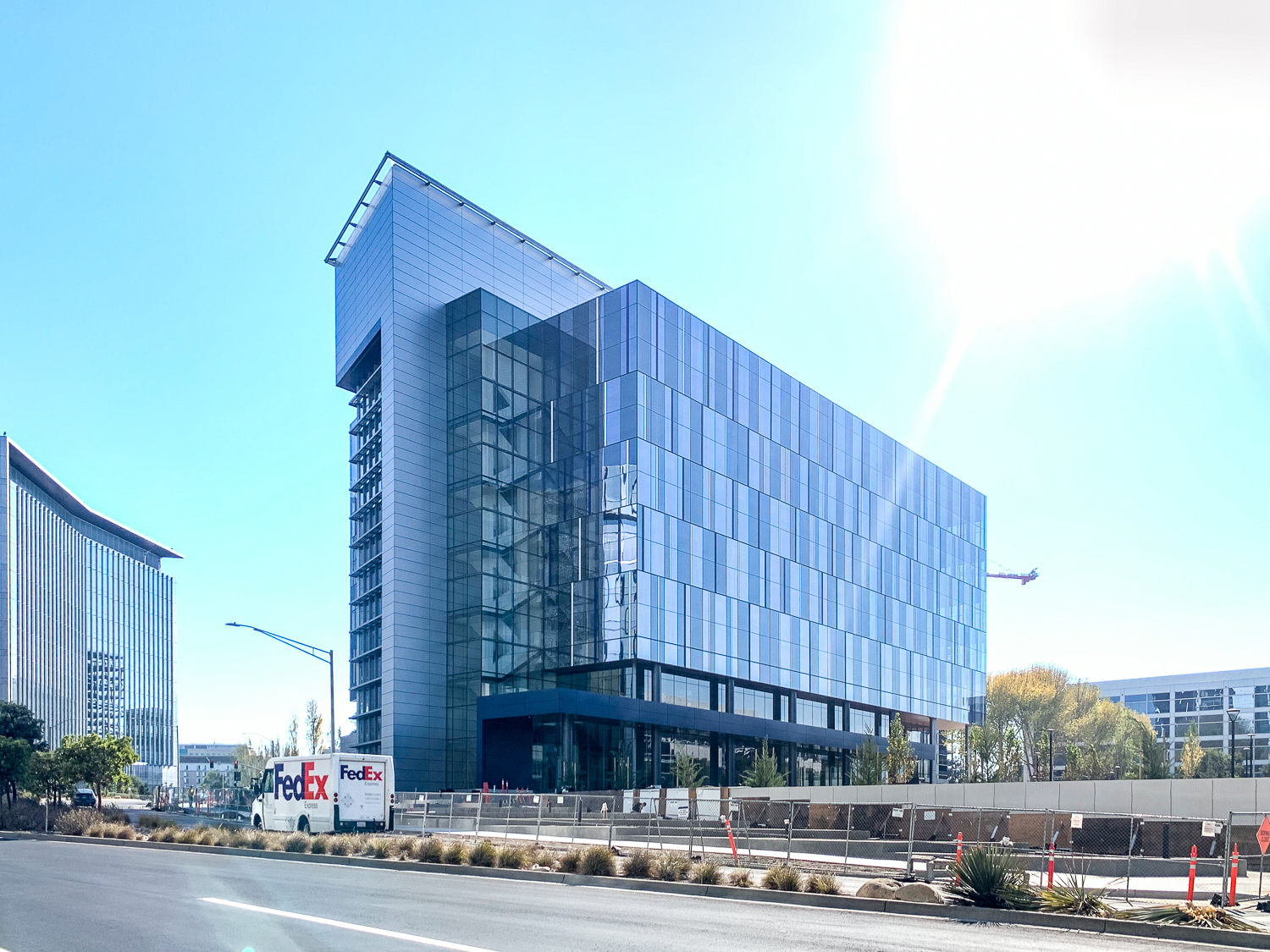
Image by Andrew Nelson
The 148-foot project contains 208,800 square feet of floor area, with seven floors and an average ceiling height of 20 feet. The design of the project (by RMW Architecture) includes a large exterior steel frame wrapped with curtain wall, glass fins, and a pixelated rain effect. There are high-end finishes utilized on both the interior and exterior of the building. Highlights of the project include a lobby that rises two floors and two interior stairwells that are visible from the exterior of the building. The stairs consist of a drywall feature running up the center and a continuous light pocket at the bottom side of the stairs.
Raymond completed interior and exterior work for DPR Construction, including metal framing, sheathing, penetration firestopping, joint sealants, gypsum board shaftwall assemblies, non-structural metal framing, plaster, gypsum board, and linear metal ceilings.
The interior portion consisted of two large supply and return mechanical shafts, three elevator shafts, three stairs running up the building, and a group of rooms dedicated to the back-of-house and a set of locker rooms on the ground floor. The project had a typical set of individual distribution frame (IDF), electrical, service, and restrooms on each of the floors.
The exterior consisted of heavy gauge framing designed to support the metal clad rain screen system. The first floor was unique and consisted of oversized soffits and canopies with light pockets, and a pump house. Levels two through seven were relatively typical with vertical bands of framing adjacent to the curtain wall systems. At the roof, there are two structures with dog-house framing and a 7000-square-foot penthouse.
As with most projects, schedule, safety, and trade stacking were typical challenges. This project was also affected by a significant weather delay. From the start, the large amount of rain from an atmospheric river washed away most grading, preventing the pouring of ground level slabs and resulting in almost two months of delay for any ground level work.
To meet the now accelerated schedule, Raymond utilized FrameCAD technology to prefabricate the exterior soffits, and the two architecturally featured stairs on the interior. In doing so, hundreds of hours were saved for each condition, compressing the duration, and allowing the General Contractor to meet their obligations.